USA PRODE DESIGN ENGINEERING
High Technology Transportation Systems for Maximum Efficiency
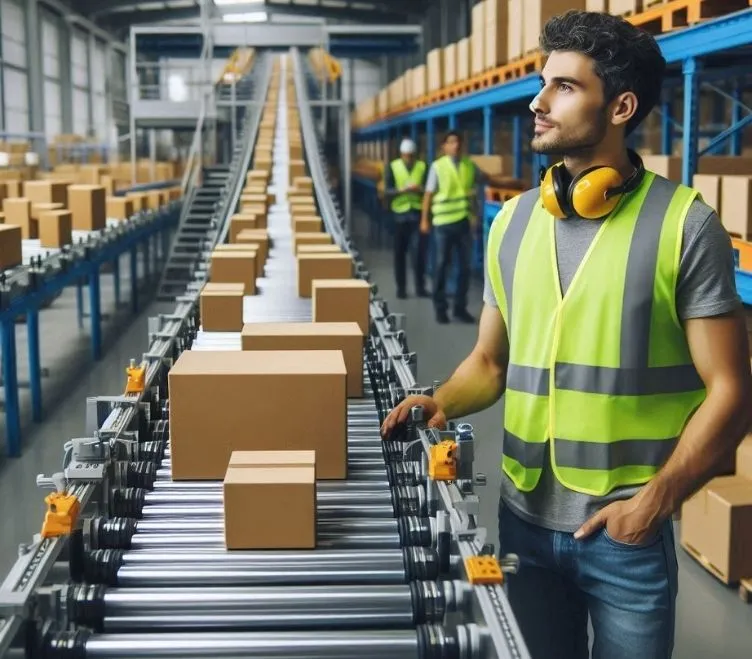
USA
PRODE
Roller Conveyors
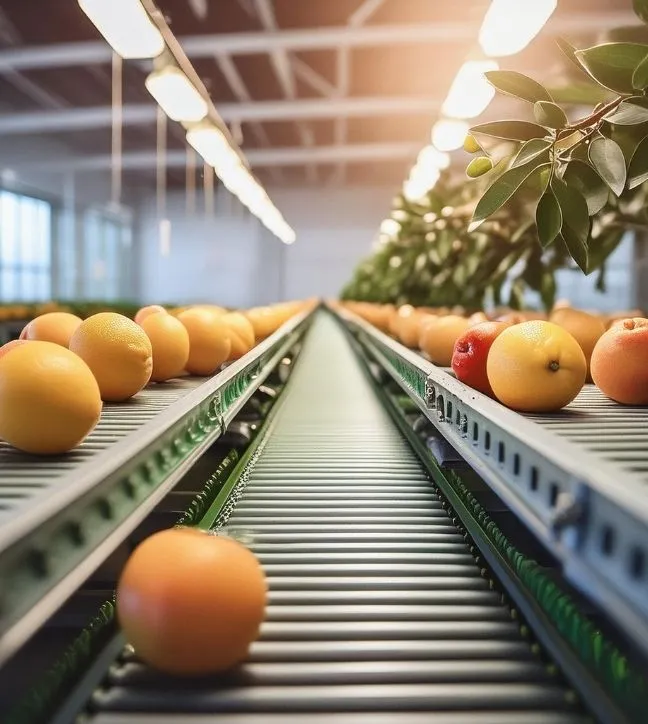
Material handling is one of the most critical elements in modern industry. Belt conveyors and idle roller conveyors stand out by providing continuous and efficient material transport. Specifically, roller conveyors are known as essential machine groups in industrial transportation systems, allowing loads to move in the desired direction on rollers. Depending on their design, they have the capacity for linear and circular load carrying. The loads to be transported are carried on rollers placed at certain intervals on the conveyor chassis. For effective conveying, the loads or the crates, pallets, and tables carrying the main load must have a flat surface.
Types of Roller Conveyors by Operation
Roller conveyors are divided into two main groups according to their operating principles: driven (powered) roller conveyors and idle (gravity) roller conveyors.
Driven (Powered) Roller Conveyors
In driven conveyors, the rollers rotate around their axes via a motor. In this system, rollers are connected to each other by elements like chains or belts, transmitting power from the motor to other rollers. Thus, the load is transported through the friction force between the rollers and the load. The roller diameters and wall thicknesses in these conveyors vary according to the weight and size of the load to be carried. Typically, the power transmission between rollers is achieved using a double row gear system.
Idle (Gravity) Roller Conveyors
In idle roller conveyors, the force is applied directly to the load. The rollers rotate through the friction created by the load moving along the conveyor. These conveyors can be designed with horizontal or inclined chassis. In horizontal designs, the driving force can be provided by pushers, but a 1-1.5% incline is recommended to facilitate load movement.
Components of Idle Roller Conveyors
An idle roller conveyor consists of three main components: rollers, the conveyor body, and conveyor legs. Due to their simple design and easy manufacturing, these conveyors are widely used in material handling. The rollers are generally made of knurled, aluminum-coated, or steel pipes. Additionally, they can be produced with polyurethane coating to achieve the desired hardness, increasing resistance to wear and chemical substances, thus ensuring long life. Rollers typically consist of a shaft with ball-bearing rollers at both ends.
The conveyor bodies and legs vary according to the load to be transported and are generally made of aluminum sigma profiles, steel angles, or U profiles.
Details of Driven (Powered) Roller Conveyors
The most distinctive feature of driven roller conveyors is that the rollers are rotated by motors and power transmission elements. These conveyors use belt or chain mechanisms for power transmission. In this system, roller diameters and wall thicknesses vary depending on the weight and size of the load to be carried. Power transmission between rollers is usually achieved using a double row gear system.
Advantages of Roller Conveyors
Roller conveyors are fundamental in modern industry and play a significant role in material handling processes. They are particularly ideal for scenarios requiring continuous material flow. Their design supports both linear and circular movements, allowing for the transportation of different load capacities and sizes. Additionally, the adaptability of these systems to the surface characteristics of the materials to be transported offers a wide range of applications.
Application Areas of Roller Conveyors
Roller conveyors are designed for use in various industries. They are well-suited for operations such as storage, packaging, assembly lines, and product sorting. Roller conveyors, categorized into powered and gravity types, provide flexibility and efficiency in transportation processes. While powered conveyors operate with the help of motors, gravity roller conveyors rely on the weight of the load itself for movement.
Considerations in Designing Roller Conveyors
For the design of gravity roller conveyors, the following information is required:
– Conveyor width
– Conveyor length
– Conveyor height
– Roller diameter and type
– Distance between roller axes
– Presence and dimensions of side barriers
– Type and dimensions of the product to be transported
– Maximum load on the conveyor
– Operating environment and temperature
For powered roller conveyors, additional considerations include:
– Motor power and speed
– Reducer housing, speed, and gear ratio
– Transmission element (chain, belt, O-ring)
– Gear system
– Conveyor speed
– Start-stop button
– Speed control panel
– Stop sensor
– Direction of operation
– Motor connection direction and shape
These details are crucial for the design and functionality of roller conveyors. Selecting the right components and designing appropriately ensures the creation of an efficient and durable material handling system.